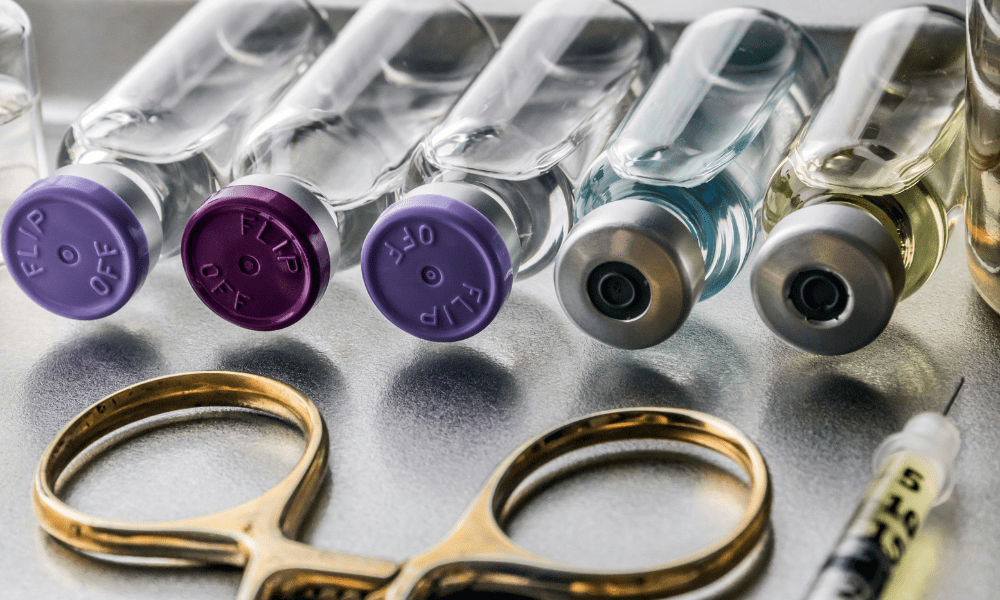
Sterility Assurance Level is typically an afterthought but can significantly impact product development schedules. Integrating sterilization strategies early on is vital for ensuring successful and timely introductions. In this article, Tony Eisenhut, CEO of NovaSterilis emphasizes the importance of considering sterilization in the early stages of R&D for new medical devices or therapeutics.
Exploring Alternatives for Effective Sterilization
Finding methods to effectively kill microorganisms without causing harm to humans and the objects being sterilized has always been challenging.
Traditional sterilization methods like heat, steam, and chemicals may not be suitable for all materials since they can damage the sterilized material. As materials become more complex and diverse, the need for alternative sterilization techniques is growing.
For over 50 years, ethylene oxide (EtO) sterilization has been the workhorse of the sterilization market. EtO is used to sterilize heat or moisture-sensitive materials that can’t be sterilized by steam sterilization. Today, more than 20 billion devices are sold in the United States annually using this type of sterilization. This represents around 50% of the devices that require terminal sterilization.
As Tony explains, because of health-related concerns and the growing complexity of medical devices, alternatives to EtO are being sought. Several alternative solutions have been developed, including supercritical carbon dioxide (scCO2) sterilization, vaporized hydrogen peroxide sterilization, hydrogen peroxide plasma sterilization, nitric oxide sterilization, and radiation-based techniques such as x-ray sterilization.
Recognizing the need for alternatives to EtO sterilization, the FDA introduced an Innovation Challenge Grant to explore the applicability and expand the use of alternative sterilization techniques in 2019. NovaSterilis was selected as one of the participants of Challenge 1 with its scCO2 sterilization technology.
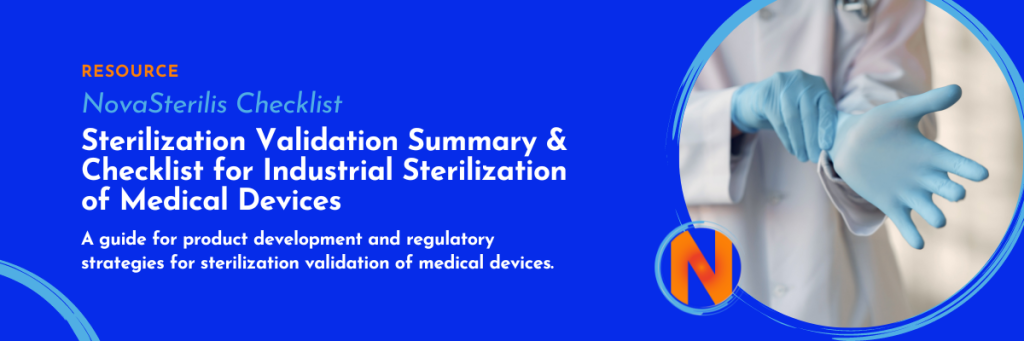
Sterility Assurance Level: The Overlooked Aspect in Medical Device R&D
Moving on to new sterilization techniques is just part of the challenge. To ensure efficient product development, it’s crucial to determine the appropriate sterilization strategy to achieve the necessary Sterility Assurance Level.
But Sterility Assurance Level has traditionally been considered an afterthought in the R&D process of medical devices. According to Tony, this has to do with where a significant portion of the early-stage research is focused at the universities.
“Academic researchers are not well versed in the realities of manufacturing and/or regulatory requirements, so often assumptions are made about what is possible. It is here that the assumption is often made that there are multiple sterilization solutions, and the commercialization partner will figure it out. What is lost in that assumption (amongst other things) is that the cost of the sterilization solution, especially if it is not terminal sterilization but rather aseptic manufacturing, may actually result in a non-commercially viable product because the cost of manufacturing is too high.” Tony says.
Industry on the other hand is more in tune with sterilization requirements. Industry decision makers often revert to historically proven techniques such as EtO and gamma irradiation. Although these techniques are the primary choice, they each have their challenges when it comes to optimal compatibility, cost, and at times, availability.
Overlooking the importance of sterilization during the early stages of product development can lead to serious consequences for companies, as explained by Tony. Some potential risks include:
- Inability to manufacture at an acceptable cost
- Profit squeeze
- Degraded performance or complete failure (some sterilization techniques may not work for certain devices due to technical or performance reasons)
“The incorporation of a terminal sterilization proof-of-concept study, whether it be industrial or academic research, is a best practice that will facilitate and streamline the commercialization of medical devices and/or drugs. A proof-of-concept study that determines material compatibility with multiple sterilization techniques, packaging options, and sterilization validation strategies (overkill vs. bioburden approach) is a cost that will enhance your ROI and save you money in the long run.”, Tony says.
The Importance of Considering Sterilization Early in R&D
Considering sterilization during the initial phases of medical device design is essential to ensure manufacturers choose the best method so that the product’s performance is not compromised.
This approach, as emphasized by Tony, offers several advantages. For instance:
- Accelerated FDA submissions – Addressing sterilization early reduces the development time, which can shorten the time to FDA application submission.
- Cost savings – Parallel tracking the evaluation of potentially viable sterilization methods can result in significant savings, specifically for startup companies.
- Higher efficiency – Incorporating sterilization into the early development process will make manufacturing processes more robust. It also allows for optimizing packaging solutions in terms of cost and ease of use. In some cases, it can even lead to improved product performance.
- Sustainability – Companies committed to sustainability and carbon neutrality can make choices aligned with their corporate goals and customer preferences.
Tony showcased an example of a client company to highlight the benefits of developing a sterilization strategy early in the R&D process to ensure the necessary Sterility Assurance Level could be achieved.
The company became aware of NovaSterilis’ scCO2 sterilization method through a published peer-reviewed journal article. They reached out to NovaSterilis to learn more about the technology and its unique attributes relative to biological scaffolds.
Based on this initial meeting, they began a series of compatibility studies, which determined that using scCO2 for a cleaning step early in the manufacturing process followed by scCO2 sterilization not only outperformed their original approach of harsh cleaning detergents followed by gamma irradiation but it also produced a product that outperformed their original design expectations.
This new product with enhanced clinical performance also performed better than the competing products already on the market. Not only was the product better performing, but it was also less expensive to manufacture because of reduced chemical costs, quicker turnaround times on the cleaning process, lower cost of sterilization, and a shorter inventory hold time due to the ability to terminally sterilize in-house.
How NovaSterilis Guides Partners Through Product Development and Sterility Assurance Level Validation
NovaSterilis collaborates with partners throughout the product development lifecycle to ensure successful introductions.
Our team starts by asking questions to assess process compatibility and the probability of receiving FDA clearance in a reasonable timeframe. They also address secondary concerns, helping partners make informed decisions about their manufacturing processes to ensure the appropriate Sterility Assurance Level is achieved, Tony says.
NovaSterilis provides helpful processes beyond sterilization, whitepapers, and services to guide partners through product development, FDA clearance, scCO2 sterilization, cost comparisons, and access to contract sterilization providers. Learn more about NovaSterilis’ services.
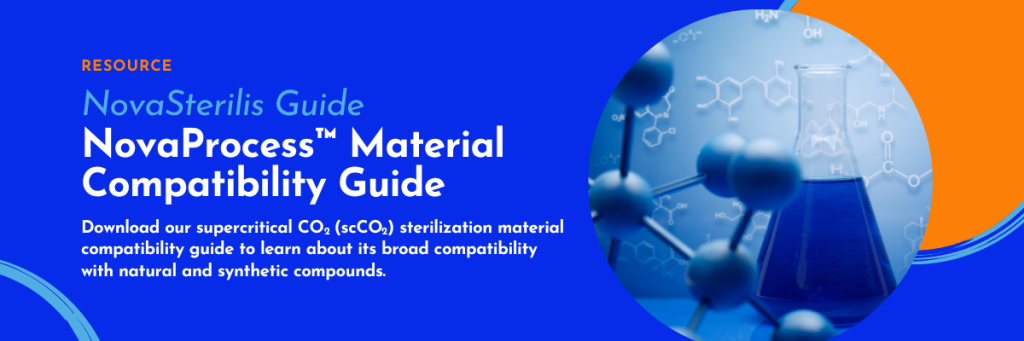